The machining process procedures of traditional machine tools in machining centers are generally the same. The main difference is that the machining center completes all cutting processes through one clamping and continuous automatic processing, so the machining center needs to perform some “after-work” after completing CNC machining.
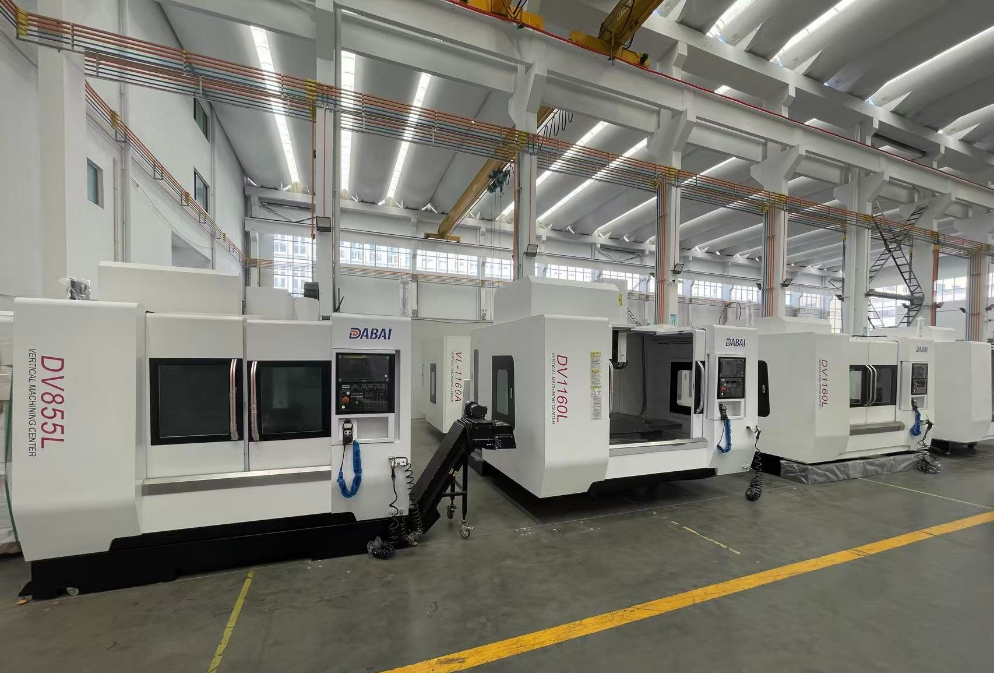
- Cleaning
After the machining center completes the cutting task, the chips should be removed in time, the machine core should be wiped, and the machine tool and the environment should be kept clean.
- Inspection and replacement of accessories
First, check the oil wiper on the guide rail. If it is worn, replace it in time.
Check the state of lubricating oil and coolant. If it is turbid, replace it in time. If it is below the scale level, add more.
- The shutdown procedure should be standardized, and the power supply on the machine tool operation panel and the main power supply should be turned off in turn.
In the absence of special circumstances and special requirements, the principle of returning to zero first, manual, jog, and automatic should be followed.
The operation of the machining center should also be low speed, medium speed, and then high speed.
The low-speed and medium-speed operation time must not be less than 2-3 minutes without abnormal conditions before starting work.
- Standardize the operation. Do not knock, correct or modify the workpiece on the chuck or the top. Make sure that the workpiece and the tool are clamped before proceeding to the next step.
The insurance and safety protection devices on the machine tool must not be disassembled or moved at will.
The most efficient processing is actually safe processing. As an efficient processing equipment, the operation of the machining center must be reasonable and standardized when it is shut down.
This is both a maintenance of the currently completed process and a preparation for the next start of work.
www.dabaicnc.com